Programmable Focus Lens
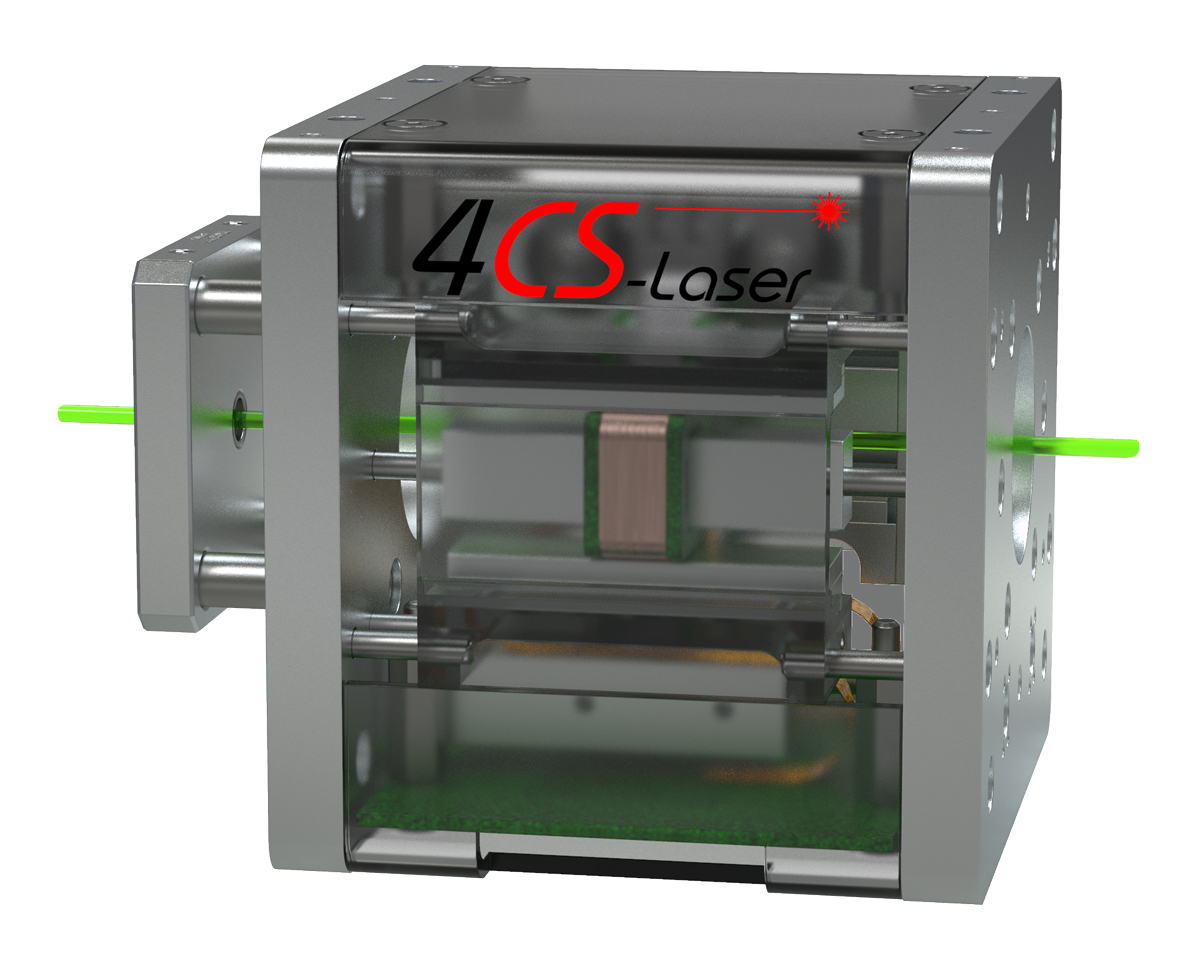
In order to get a perfect laser cut, a laser beam must travel through a chain of serially aligned optical elements. This optical chain usually consists of a beam expander, a focus lens, a galvo/scanner and an f-theta lens. Only if all these elements are perfectly aligned to each other, a perfect laser cut can be achieved.
For technical reasons, focussing of the laser beam is normally done with the last optical element. Depending on the application, however, modifications of some of the optical elements might be necessary. Laser trimming of a resistor, for example, requires a very narrow laser focus. The focus used for a labelling process, on the other hand, must be large in order to allow for a high process speed.
Depending on the incident angle, small (<1mm) z-height variations of the workpiece can lead to unsatisfactory results of the laser cut. If the surface is outside the focus depth, material ablation reduces significantly. This has a negative impact on process quality. When trimming a resistor, scattering of the cutting width from sample to sample makes process set-up very difficult. In some cases, one may compensate this effect by increasing the laser power. This increases also the width of the laser cut, however, which may lead to other negative impacts on the results.
After spending many hours with process optimizations, we came to the conclusion, that a programmable laser beam focus is indispensable for stable production. We developed a Focus lens unit for 1’’ lenses, that can be precisely adjusted electromechanically at high speed. A controller is used to accurately position the lens along the beam with a resolution of 1µm within a working range of +/- 25mm.
Using the programmable focus lens unit, z-height variations can be considered, by adapting the focus of the beam in real time. The z-height must be known, however. It can, for example, be measured using a laser distance sensor integrated in the laser system. Furthermore, using a programmable focus lens, also costs for time consuming setup procedures can be saved, since focus setting can be stored as a recipe parameter for each product.
Finally, since the laser focus can be set in real time, also laser processing of free form surfaces is no longer only a wish but reality.
The advantages for the end user are obvious:
- Short setup time
- Robust laser processing and higher quality
- Laser cutting or machining of free form surfaces
Contact
Legal
Social
4CS-Laser AG
Turmstrasse 18
CH-6312 Steinhausen/ Zug
+41 (0) 41 747 18 66
Contact
4CS-Laser AG
Turmstrasse 18
CH-6312 Steinhausen/ Zug
+41 (0) 41 747 18 66